What we do?
We coat, perforate, profile and customize products for the construction of exhaust systems.
And in the form of domes with a wide range of dimensions. These are hollow forms that are driven into a metal sheet. Hence our name: simple and straightforward, but highly efficient – Kalotte AG.
non-binding requestSound-absorbing heat protection
Our materials: micro-perforated and dimpled, partly heat-sealed foils and tapes made of stainless steel and aluminum. The benefit? Our products are used as sound-absorbing heat shields. And: the profiling that we do increases the rigidity.
Increase in rigidity
If the carrier material is profiled, its total surface area increases, which leads to greater inherent rigidity.
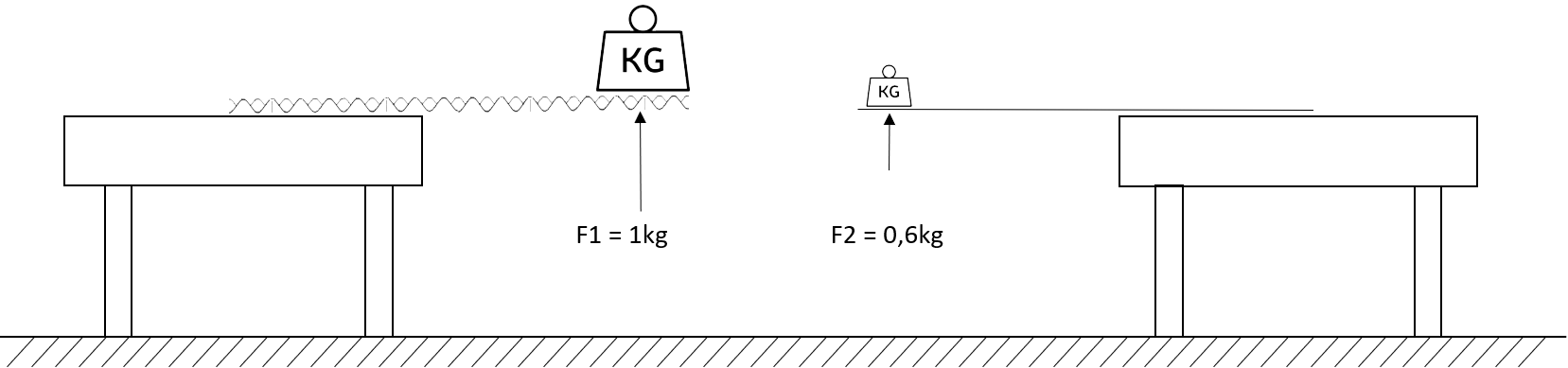
And where are our products used?
In the automotive industry, in the engine compartment, on and in the exhaust system, and wherever heat is generated. Kalotte products can also be found in the white goods industry, in energy storage, and in efficient heat and power generation.
Kalotte – a valuable player in the future, too.
Yesterday – today – tomorrow
And that is what makes us so valuable: our products are not dependent on any trends.
Whether combustion engine, electric motor or future technologies – our profiles fulfill their function in all devices. Reliable and high-quality.
Kalotte – a valuable player in the future, too.
Our process
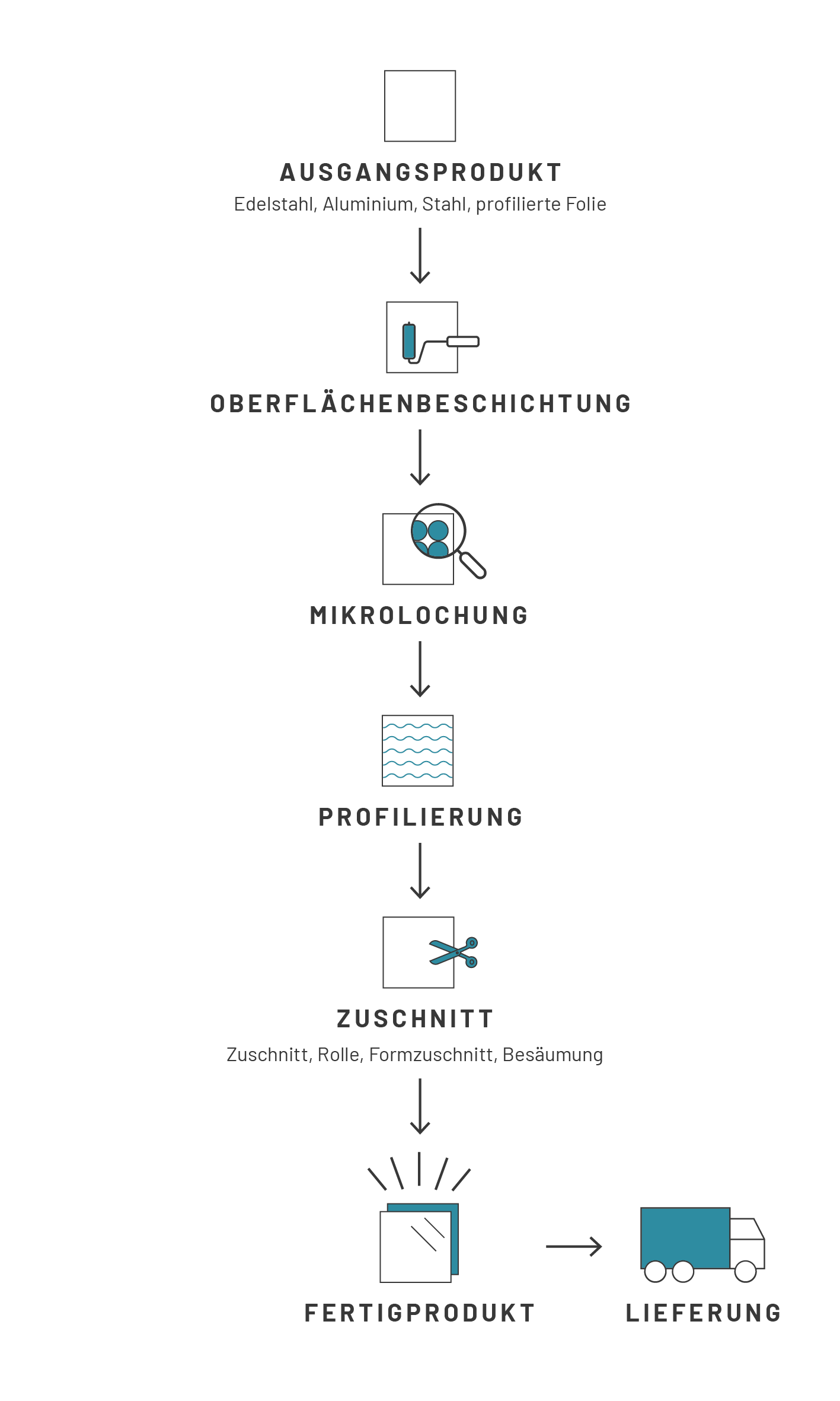
Step 1
Coating
During coating, we melt the thermoplastic coating layer. This creates an adhesive bond between the substrate and the carrier film. The benefit? Together with the carrier sheet, a sound-absorbing heat shield is created, i.e. an acoustically and thermally effective insulation layer. On the side facing away from the sound source, there is a protective film with micro-perforations.
Step 2
Micropunching / perforation
In further steps, the carrier materials (heat-seal film, stainless steel, aluminum, steel) are perforated in the micro range of 0.1 – 1 mm, after which profiling is carried out. The universal product then enters the process defined by the customer. After delivery to the customer, the customer can go directly into production to complete the exhaust system or parts of it. Important cost-intensive process steps are outsourced to us.
Microperforierung
- 1 – 40 holes/cm2
- possible in all versions
- from 0.1 – 1 mm
Step 3
Profiling / calotte milling
Geometry
- hollow form hammered out of sheet metal
- spherical cut
- curved surface of a spherical segment
- semi-dome-shaped curvature
- sine circles
- 2 sine curves
- 45° offset from each other
- 1 offset
Product code
Fine calotte UP 200 – 300 4.0 x 0.6 mm
Small dome XP 200 – 400 2.5 x 1.8 mm
Dome P 200 – 400 4.5 x 2.5 mm
Large dome GSP 200 – 300 8.0 x 3.5 mm
Worm structure WS 20 – 60 x 0.6 mm
Coarse grain | Stucco
Step 4
Parts in the desired form
JIT products:
parts from 10 x 21 to 1,250 x 4,000 mm
Roll material
20 – 1000 kg
from 200 – 1270 mm width
large and small coils as semi-finished products for direct coil processing in a press line
Freely selectable coil width
Slitting and trimming
Slitting of coils / foils / strips from 0.05 – 0.8 mm
Trimming (cutting) and separating of foils
and strips
Step 5
Delivery from stock
Short delivery times thanks to the storage of the most common materials; 1,000 tons in stock
Consignment stock, purpose- and production-related processes
Uncomplicated processing
Emergency delivery within a few hours